Medical & Pharmaceutical
Sepro Group, the clean room challenge
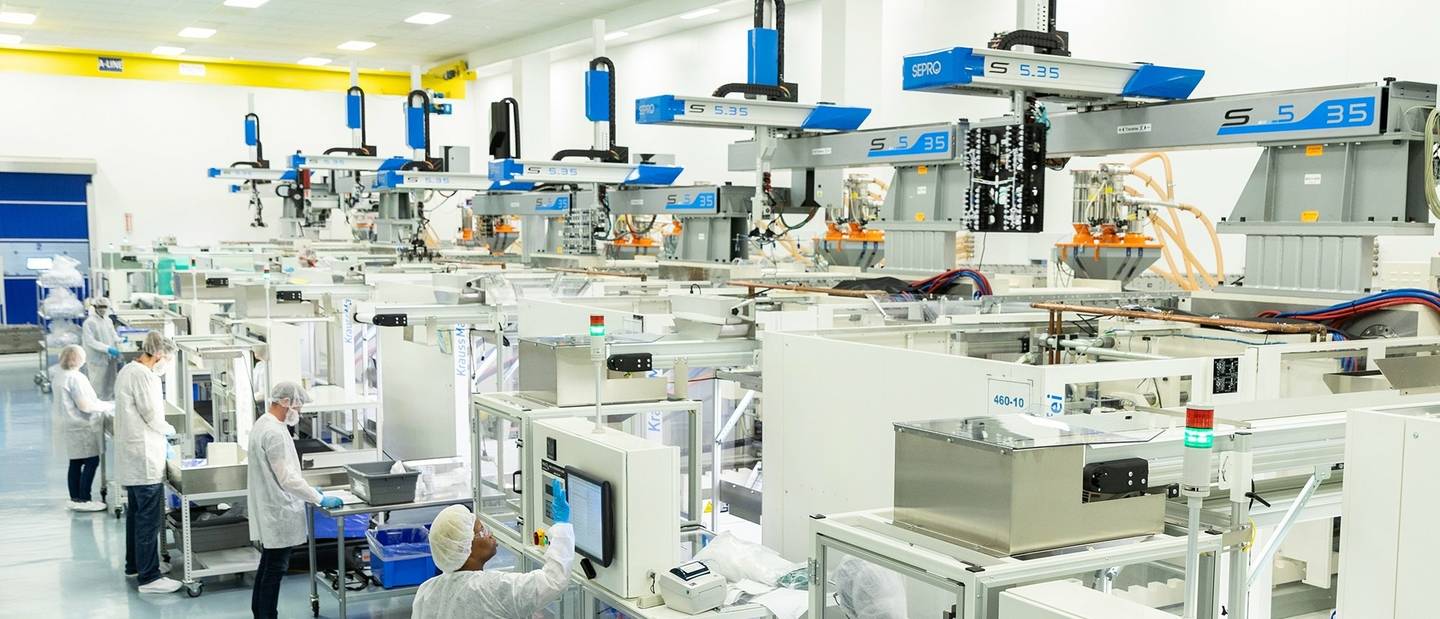
Sepro robots increase productivity and enhance workflows. Within cleanroom market, our robots can be used with the injection molding machines and with their peripherals: assembly, inspection, traceability, packaging, etc. Sepro has launched a dedicated range.
Fischer Söhne serves a wide range of customers from the medical, pharmaceutical, packaging and industrial markets. With production based on BRC, hygiene and clean room requirements, no compromise is possible. With Sepro robots, we can increase our productivity while guaranteeing an optimal level of hygiene. Sepro is a responsive company, with fast delivery times and flexibility
Iwan Tresch
CEO - Fischer Söhne
Robots are more and more integrated within clean rooms. They help to improve efficiency, to stabilize the process, and to enhance workflow. Injection-molding robots can meet all but the most stringent requirements. In fact, they can exceed the level of cleanliness possible with injection-molding processes.
In a clean room, Sepro Group guarantees:
Our cartesian robots can be adapted to the clean room environment. All the areas where grease or other lubrication are necessary are perfectly sealed. All cables are protected in conduits and pneumatic air is filtered to 0.3 micron. All surfaces are smooth to make cleaning easier. Material in contact with moulded parts selected to meet customer specific requirement : anodized aluminium, nylon, stainless steel, etc.
The S5 Line is designed using the best Sepro technology, to make a very well-designed range of high performance 3-axis robots. They are reliable, fast and precise and ideal for complex applications.
5X Line robots are designed from latest generation fast and precise Sepro 3-axis Cartesian robots with a Stäubli 2-axis servo wrist. A unique combination that provides a number of solutions for automating injection molding machines. These robots installed on the IMM can be used for unloading and processing parts; they can be located at the end of the IMM to perform post-processing. They can be programmed quickly and efficiently thanks to the power and user friendliness of the Visual 3 control system.