
New options in multi-axis robots for plastics injection molding
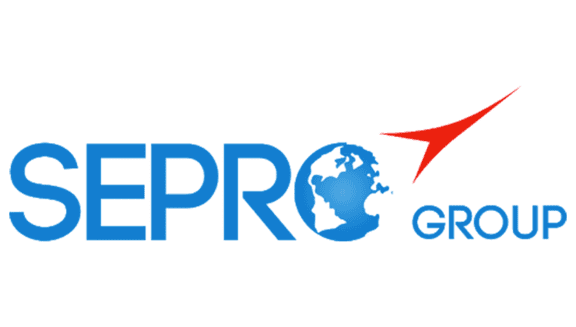
When considering the purchase of an automobile, a buyer might question the advantages of four-wheel drive versus two-wheel drive, or whether one model has more leg room than another. The buyer is not so much asking if one car is better than another but rather trying to determine which car is easier to handle in ice and snow or which will be more comfortable for a tall person to drive. It’s the same when an injection molder asks about different robot configurations. With so many choices available to molders today, it is important to understand the pros and cons of each design.
ROBOTS FOR INJECTION MOLDERS
The 3-axis Cartesian beam robot (sometimes called a gantry robot) is the workhorse of injection-molding automation. Unlike 6-axis articulated arm robots and simpler devices like SCARA robots, which can be used in almost any industrial application, Cartesian robots are configured mainly to meet the unique needs of injection molding. Cartesian robots get their name from the French philosopher and mathematician René Descartes, who used three basic X, Y and Z axes to define space. These robots all have a vertical Z axis that allows it to reach into the space between mold halves, an X axis that is defined by the horizontal beam that normally reaches from an area above the mold to a point outside the machine, and a Y axis that moves the vertical arm in-line with the machine to strip parts off of mold cores or position them outside the molding area. If you need a robot simply to remove a part from the molding machine so as to allow rapid, repeatable cycling, a 3-axis robot is probably all you need. It is only when you need to ask more of the robot – additional manipulation options inside the mold or outside the machine that you need to start thinking about advanced 3-, 5- or 6-axis robots. At the other end of the spectrum, 6-axis articulated robots have an arm that is similar, in many ways, to the human arm. It can rotate around its base like the human limb rotates around the shoulder. It can bend in the middle like a human elbow and it has a wrist that can rotate and move the hand in an up-and-down arc. Thus, an articulated-arm robot can grip an object at almost any angle and at almost any point within its reach. Some of the same motions have been built in the 3-axis robot wrist using pneumatic actuation. These are what Sepro calls the R1 and R2 rotations and they move the wrist from 0° to 90° or 0° to 180° without any intermediate stops. However, depending on how much additional automation is built into a molding cell – insert feeders, or gaging, deflashing, welding or decorating devices, for instance – the addition of pneumatic wrist rotations to simple 3-axis robots can allow them to be part of automated systems that are quite complex.
5-AXIS SERVO ROBOTS
In October 2012, Sepro introduced its 5X Line of robots with 5 servo-driven axes of motion. It offers many of the same parts-handling capabilities as a 6-axis articulated arm robot, but does so in a configuration that will be familiar to anyone who has used 3-axis robots. The X, Y and Z axes are identical. It is the servo wrist at the end of the vertical arm that makes the difference. The R1 and R2 motions are available, but instead of having to move through the full 0° to 90° or 0° to 180° swings, the servo wrist can move through any portion of those arcs at any time, and the movements can all be executed simultaneously. In fact, the robot can move in all 5 axes at any time with complete control. The secret is in the servos. Under pneumatic power, a valve opens to allow air pressure to move the wrist, which will continue to move until it reaches a hard stop that shuts the valve and cuts power. A servo motor, on the other hand, has a positional encoder that recognizes exactly where the drive shaft is at any moment. The system control is then able to integrate positional signals from all of the servo motors on all 5 axes so that it knows exactly where the gripper and part are in space at all times. This allows the robot to complete very complicated motions very precisely and with perfect repeatability. If you have a complex part that can’t be ejected from the core in a straight line, or if you have limited space between mold halves or tie bars, it may be necessary to rotate a part before it can be lifted out of the machine. The servo wrist is able to make those multi-axis movements in the same way that the human hand and wrist would do it, but with much greater speed and precision. Once the part is out the mold, it may be necessary to perform secondary operations like glue application and assembly or edge-flaming to remove flash. Without releasing the part, the 5-axis robot can move it with precision past a stationary flame source or glue head. This is far more efficient than having a human operator perform these functions or placing the part in a fixture so that some other piece of automation can execute the secondary operations. Today’s servo-driven 5-axis Cartesian robots have the advantage of top-entry speed for shorter cycle times as well as the flexibility inside and outside the mold of an articulated-arm robot. Thus, 5-axis robots can perform many of the complex part-manipulation tasks historically assigned to 6-axis articulated arm units.
6-AXIS ARTICULATED-ARM ROBOTS
One of major concerns about using articulated-arm robots in injection molding has always been the complexity of their programming and control systems. Even straight-line movement of an articulated-arm robot requires coordination of several different articulated joints. Some molders feel they need specially trained personnel to handle the programming and maintenance of these robots. That changed a year ago when, at the same time it introduced the 5X Line of Cartesian robots, Sepro also introduced as 6X Line of articulated arm units adapted to use the same control systems as its Cartesian robots. Using “simple pick and place” programming, the user only needs to identify step-by-step the different points and positions in the robot cycle (picking, quality inspection, unloading, stacking, etc.). Then the operator manually “teaches” the robot the path between each point and the trajectory (either straight-line or curvilinear) is automatically computed. Thus, injection molders today will find 6-axis robots much easier to program and operate than in the past. They can now evaluate Cartesian and articulated-arm configurations solely on the basis of which suits their application best.
PROS & CONS
The big difference between 5-axis and 6-axis robots is the addition of 360° reach. Cartesian robots are restricted to movement in line with or perpendicular to the molding machine. A longer beam can add side reach or, when they are installed in an axial configuration (with the long X-axis beam extending along the top of the machine), they can unload parts at the end of the molding machine, potentially allowing molding machines to be positioned closer together or otherwise optimizing the use of floor space. Cartesian robots are normally mounted on top of the fixed platen. Consequently, they cannot reach forward to the injection end of the machine. A 6-axis robot, on the other hand, has a larger working envelope since it has equal reach in all directions. Because they are not mounted on top of the molding machine like beam robots, they may be the only automation solution for plants with limited overhead space. Since they normally enter the mold area from the side rather than the top, the way Cartesian beam robots do, articulated arm units may be better for vertical-clamp insert molding. Their movement is not limited by the vertical clamp and they can easily reach multiple stations on the rotary tables often found on those machines. Advantages, however, can become limitations in different circumstances. Floor-mounting is good when ceiling heights are low, but problematic when space around the machine is limited. Side-entry usually limits 6-axis robots to the back of the machine, where they will not interfere with access to the operator control panel. With a Cartesian robot, there is easier access to either side of the machine. The speed of articulated-arm robots has increased in recent years to a point where it is comparable in many motions, but beam robots are generally regarded as being faster at moving into and out of the mold space to retrieve parts. This could be a critical factor in some fast-cycle applications. Lastly, there is the issue of cost. As a general rule, a Cartesian robot – even with the addition of the servo-driven wrist– is going to be about 30% less costly than an articulated-arm unit. None of these factors should be taken to mean that one configuration is better or worse than the other. It really depends on the unique conditions that exist in each molding plant and apply to specific applications. Cartesian and articulated-arm robots are sometimes even used together. The machine-mounted beam robot picks the part and presents it to the articulated-arm unit for secondary operations. This may be the ideal set-up when molding cycles are relatively short and downstream functions are especially numerous, complicated or time-consuming. Thanks to new technology from Sepro, its partners and other suppliers, injection molders today have more choice than ever when it comes to automating their process. More choice, however, also adds complexity to the process of deciding what features and capabilities are required. So, just as you would enlist the help of a knowledgeable and reputable dealer to assist in the purchase of a car, it is important to seek the informed counsel of a reliable supplier for help in selecting which robot is right for you. By Scott Kendrick, Product Project Manager, Sepro Robotique
Stay connected
Receive a summary of our news and events every month